The main drawbacks of direct extrusion are limited material choices, potential for surface defects, and difficulty in achieving complex shapes.
Overview of Direct Extrusion Process
Defining Direct Extrusion
Direct extrusion, commonly known as forward extrusion, is a method where manufacturers force material through a die to create objects with a consistent cross-sectional profile. This technique involves placing a material billet in a chamber and then using a hydraulic or mechanical press to push it through a die positioned at the opposite end. This approach is essential in manufacturing for producing items like metal bars, tubes, and varied profiles, offering versatility in product design.
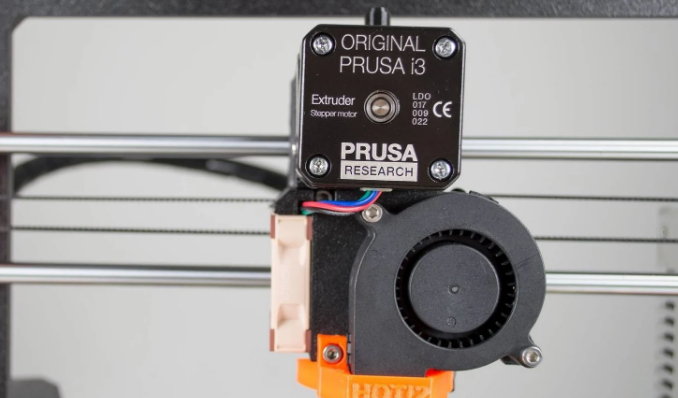
The Mechanism and Its Industrial Applications
The direct extrusion process incorporates several critical components:
Extrusion Press: Manufacturers use presses with force ranging from 100 to 15,000 metric tons, which directly affects operational costs and output capabilities.
Die and Chamber Design: The die’s shape is crucial as it defines the product’s cross-section, while the chamber needs to handle high temperatures and pressures efficiently.
Temperature Management: Maintaining specific temperatures, typically between 350°C to 550°C for metals like aluminum and steel, is vital to preserve the material’s properties during the process.
In industrial contexts, direct extrusion is a popular choice due to its ability to form complex cross-sections with fine surface finishes. It finds extensive use in the metal industry, especially with aluminum and copper, and is also applicable to plastics and polymers.
The process efficiency, in terms of material usage and production speed, largely depends on the material type and the complexity of the profile being extruded. While it is effective in conserving material, direct extrusion might be slower and more energy-consuming compared to alternative methods like indirect extrusion.
For further exploration of direct extrusion and its applications, you can check Direct Extrusion on Wikipedia.
High Equipment Stress and Wear in Direct Extrusion
Impact on Machinery Longevity
Direct extrusion subjects equipment to intense stress. This stress, resulting from high pressure and friction, mainly affects the die and chamber. It can significantly shorten machinery lifespan. Machines processing harder materials, like certain metals, often wear out faster than those handling softer materials.
Maintenance and Replacement Costs
High stress demands frequent maintenance, which is essential for efficiency and extending the equipment’s life. Routine checks and part replacements, such as for a worn die or a damaged press, can be costly. These expenses affect the production budget directly.
Regular maintenance and part replacements add to operational costs. They include the costs of parts, labor, and production downtime. Time spent on repairs can delay production, increasing costs further.
For detailed insights into equipment stress effects in direct extrusion, see Extrusion Equipment Maintenance on Wikipedia.
Material Limitations and Challenges in Direct Extrusion
Restrictions on Types of Materials Used
Direct extrusion faces limitations in the types of materials it can process effectively. The method is ideally suited for softer metals like aluminum and copper, and specific polymers like Polyethylene (PE) and Polyvinyl Chloride (PVC). However, working with harder metals, such as steel and titanium, poses challenges due to their higher melting points and strength. These materials require more power for extrusion, thus increasing operational costs. The extrusion machinery must also be capable of handling the increased stress and temperatures, necessitating robust and often more expensive equipment.
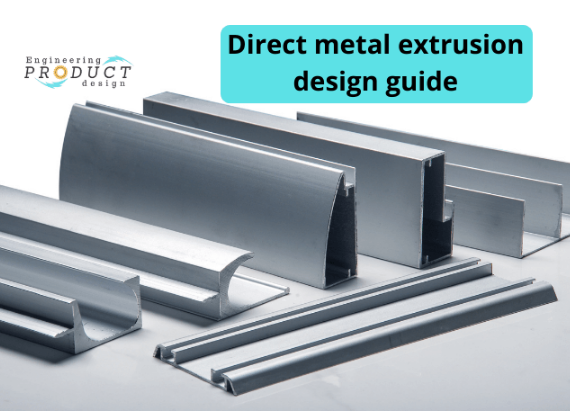
Difficulties in Extruding Certain Alloys and Polymers
Extruding certain alloys and polymers also presents unique challenges. Alloys with complex compositions might require precise temperature control to maintain their properties during extrusion. For example, aerospace-grade alloys demand tight tolerances that can be difficult to achieve in direct extrusion. Similarly, some high-performance polymers, known for their heat resistance, can be challenging to extrude due to their high melting points and sensitivity to temperature changes. This necessitates specialized machinery and can lead to slower production speeds and higher costs.
The process efficiency and quality of the extruded products are heavily influenced by these material characteristics. Manufacturers must carefully consider the material properties, balancing the costs and benefits to achieve the desired quality and performance.
For a deeper understanding of these challenges, visit the Direct Extrusion Material Limitations page on Wikipedia.
Operational and Energy Efficiency Issues in Direct Extrusion
Increased Power Consumption
Aspect | Details |
---|---|
Power Requirement | Direct extrusion requires high power, often ranging from 100 to 1000 kW |
Cost Implication | Increased energy consumption leads to higher operational costs |
Comparison | Consumes more power than indirect extrusion or other manufacturing processes |
Impact | High power requirement can limit the process’s feasibility for smaller operations |
Lower Production Speeds Compared to Other Methods
Aspect | Details |
---|---|
Speed of Production | Generally slower than indirect extrusion |
Material Impact | Harder materials further reduce the speed, affecting throughput |
Cost Implication | Slower speeds result in longer production times, increasing labor and overhead costs |
Comparison with Other Methods | Methods like injection molding or indirect extrusion often achieve higher speeds |
Direct extrusion’s operational and energy efficiency issues directly influence its cost-effectiveness and suitability for different applications. The process requires balancing the benefits of direct extrusion against its higher power consumption and slower production speeds.
For more information about the efficiency challenges in direct extrusion, explore related articles on Direct Extrusion Efficiency on Wikipedia.