Yes, melamine is commonly injection-molded, especially for creating durable tableware and kitchen utensils.
Understanding Melamine in Injection Molding
Melamine, a thermosetting plastic, is renowned for its heat resistance and surface hardness, making it a popular choice in injection molding for a variety of applications.
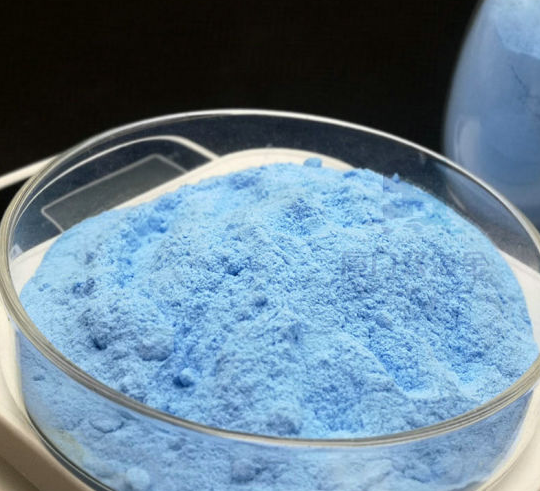
Properties of Melamine as a Molding Material
Key Characteristics:
Heat Resistance: Melamine can withstand temperatures up to 356°F (180°C), making it suitable for high-heat applications.
Surface Hardness: Known for its hard and glossy finish, melamine is resistant to scratches and stains.
Electrical Insulation: It offers excellent electrical insulating properties.
Chemical Resistance: Resistant to acids, bases, and organic solvents.
Advantages:
Durability: Highly durable, suitable for long-term use.
Aesthetics: Provides a high-quality finish, available in various colors and patterns.
Limitations:
Cost: Higher cost compared to some other thermoplastics due to its properties and production process.
Molding Conditions: Requires precise control of temperature and pressure during molding.
Historical Use of Melamine in Injection Molding
Evolution Over Time:
Early Adoption: First used in the 1930s, melamine gained popularity for its heat-resistant tableware.
Post-War Expansion: The post-WWII era saw an expansion in its use, including electrical and automotive applications.
Modern Innovations: Recent advancements have improved the efficiency and quality of melamine injection molding, expanding its use in various industries.
Production Efficiency:
Energy Requirements: The molding process for melamine is energy-intensive due to high-temperature and pressure requirements.
Production Speed: Typically slower than thermoplastics due to the curing time of thermosetting polymers.
For more detailed information on melamine and its use in injection molding, refer to Melamine on Wikipedia.
Identification of Injection Molded Melamine Products
Identifying injection molded melamine products involves a close examination of their visual and physical characteristics, as well as understanding how these features differ from products manufactured using other processes.
Visual and Physical Characteristics of Injection Molded Melamine
Key Features:
High Gloss Finish: Melamine products typically exhibit a shiny, high-gloss surface.
Hard and Smooth Texture: The surface is hard to the touch, with a smooth texture.
Color and Design: Melamine allows for a wide range of colors and intricate designs.
Weight and Density: Melamine items have a substantial feel, indicating higher density compared to some other plastics.
Durability Aspects:
Scratch Resistance: The surface is highly resistant to scratches and abrasions.
Heat Resistance: Melamine retains its form and color even when exposed to high temperatures.
Differentiating Injection Molded Melamine from Other Processes
Comparison with Other Plastics:
Thermosetting vs. Thermoplastic: Unlike thermoplastics, melamine (a thermosetting plastic) does not soften upon reheating.
Surface Quality: Melamine’s surface is usually more rigid and glossy than products made with other plastics.
Cost and Production Efficiency:
Manufacturing Cost: The cost of producing melamine products is generally higher due to the material and specific process requirements.
Production Speed: The curing process in melamine injection molding is slower compared to thermoplastics.
For a deeper exploration of melamine and its properties, visit Melamine Resin on Wikipedia.
The Injection Molding Process of Melamine
The injection molding process of melamine is distinct due to the material’s unique properties. This section explores the steps involved in molding melamine and addresses the technical challenges and solutions associated with this process.
Overview of Melamine Injection Molding Steps
Key Stages:
Material Preparation: Melamine resin is prepared, often mixed with fillers and colors.
Melting and Injection: The material is heated and injected into the mold under high pressure.
Curing and Cooling: Melamine undergoes a curing process within the mold to set its final form.
Ejection and Post-Processing: The cured product is ejected, and any necessary post-processing, like trimming, is performed.
Production Efficiency:
Cycle Time: Due to curing, cycle times are longer compared to thermoplastics.
Energy Usage: High temperatures and pressures increase energy consumption.
Technical Challenges and Solutions in Melamine Injection Molding
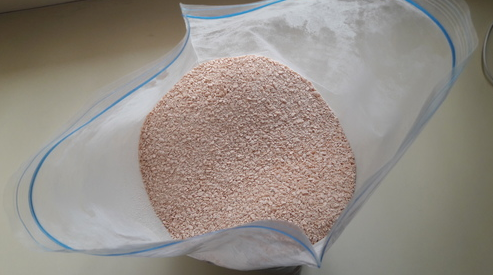
Challenges:
High Heat and Pressure: Melamine requires high heat and pressure for proper molding, which can be demanding on equipment.
Curing Time: The curing process requires precise timing to ensure product integrity.
Mold Design: Complex geometries can be challenging due to melamine’s rigidity after curing.
Solutions:
Advanced Machinery: Using specialized injection molding machines capable of handling high pressures and temperatures.
Mold Release Agents: Applying mold release agents to facilitate easier ejection and extend mold life.
Process Control: Implementing precise control over temperature, pressure, and curing time to ensure consistency and quality.
For further details on the melamine injection molding process, refer to Injection Molding Process on Wikipedia.
Quality and Safety Aspects of Injection Molded Melamine
The quality and safety of injection molded melamine products are governed by rigorous testing protocols and compliance with established safety standards and regulations. Below is a detailed overview structured in a tabular format.
Testing and Quality Control for Melamine Products
Aspect | Details | Impact |
---|---|---|
Strength Testing | Assessing the mechanical strength to ensure durability. | Ensures the product can withstand everyday use. |
Heat Resistance Test | Evaluating the ability to resist deformation and discoloration at high temperatures. | Critical for kitchenware and high-heat applications. |
Chemical Analysis | Testing for chemical composition to confirm purity and safety. | Ensures no harmful substances are present. |
Surface Inspection | Checking for uniformity in color and glossiness. | Important for aesthetic and functional quality. |
Dimensional Accuracy | Measuring dimensions to ensure they meet specified tolerances. | Ensures compatibility and functionality in end-use. |
Safety Standards and Regulations for Melamine in Injection Molding
Standard/Regulation | Description | Relevance |
---|---|---|
FDA Regulations | Guidelines for safe use in food-contact products. | Ensures melamine products are safe for food-related uses. |
EU Safety Standards | Compliance with EU regulations for chemical composition and migration. | Mandatory for products sold in the European market. |
ISO Quality Standards | Adherence to international quality management principles. | Guarantees consistent product quality and safety. |
Environmental Compliance | Regulations on emissions and waste management during production. | Ensures environmentally responsible manufacturing processes. |
Consumer Product Safety | Standards for product safety, especially in children’s items. | Prevents hazards in products used by vulnerable populations. |
Cost and Efficiency Considerations:
Testing Costs: Rigorous testing can add to the overall cost of production.
Efficiency: Streamlined quality control processes can enhance production efficiency and reduce waste.
Market Competitiveness: Compliance with safety standards is crucial for market access and consumer trust.
For more insights into these standards, visit Melamine Safety on Wikipedia.