There are two primary types of injection molding: “thermoplastic injection molding” and “thermoset injection molding,” each suited to different materials and applications.
Types of Injection Molding
Injection molding, a versatile method, is extensively used for producing plastic parts and components. This process involves injecting molten material into a mold, creating products with precise dimensions and complex shapes. Below we delve into various types of injection molding, emphasizing their specific characteristics, advantages, and drawbacks.
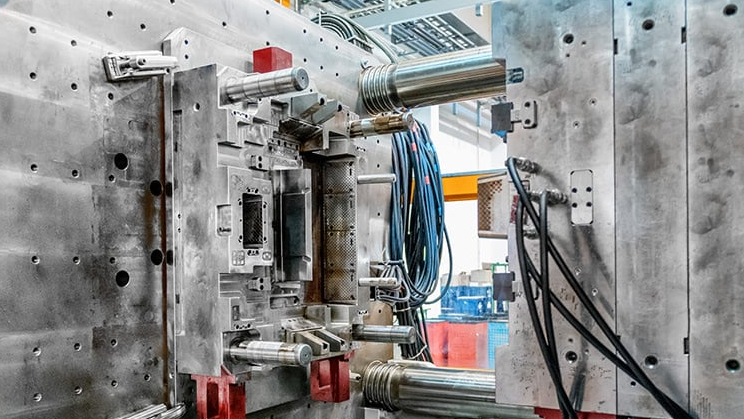
Thermoplastic Injection Molding
Thermoplastic injection molding is prevalent in the industry, utilizing polymers that melt upon heating and solidify when cooled. It is renowned for its efficiency and speed, making it ideal for mass production. Typically, manufacturers opt for thermoplastics like polyethylene and polystyrene due to their versatility in color and texture. Consequently, the range of products includes everything from household items to medical components. Although this method is cost-effective, it requires a significant initial investment in machinery and molds.
Key Characteristics:
The production speed of these machines is a major advantage, reducing production time considerably.
Reusability is another benefit, as thermoplastics can be reheated and reshaped, promoting recycling and waste reduction.
However, these machines consume substantial power, affecting operational costs and environmental considerations.
Thermosetting Plastic Molding
Transitioning to thermosetting plastic molding, this method uses plastics that harden permanently after heating. Materials like epoxy and phenolic resin, common in this process, are known for their durability and resistance to heat. This makes them suitable for products like electrical insulators and automotive parts. A limitation, however, is the irreversible nature of the curing process, leading to potential material waste, and the non-recyclable nature of these materials.
Key Considerations:
Products made from thermosetting plastics can endure higher temperatures than those from thermoplastics, offering greater suitability for high-heat applications.
The inflexibility of these materials, once set, limits their reusability, as they cannot be remelted or reshaped.
Overmolding and Insert Molding
Meanwhile, overmolding and insert molding blend multiple materials to create a single part. Overmolding typically employs a hard plastic base with a softer material like rubber layered on top, ideal for tool grips or toothbrushes. Conversely, insert molding integrates metal or other materials into the plastic. Although these methods enhance product functionality and aesthetic appeal, they necessitate precise control and complex machinery, leading to increased production costs.
Distinctive Features:
The combination of materials in these methods results in products with enhanced strength, aesthetics, and functionality.
Yet, they require meticulous planning, design, and specialized equipment.
Micro Injection Molding
Lastly, micro injection molding focuses on producing extremely small and precise components, frequently used in medical devices and microelectronics. This process demands high precision and specialized equipment, capable of handling tiny amounts of material with extreme accuracy. The trade-off here is the limited size range and the need for specialized polymers, which can escalate costs.
Critical Aspects:
Suitable for parts requiring intricate details and tight tolerances, this method is a testament to the precision achievable in modern manufacturing.
It often calls for materials with specific properties, tailored for micro-scale manufacturing.
For a deeper understanding, refer to Injection Molding on Wikipedia.
Materials Used in Injection Molding
Injection molding, a key process in manufacturing, uses a variety of materials, each with unique properties and applications. The choice of material significantly impacts the product’s quality, cost, and performance. Here, we explore the primary materials used in injection molding: polymers and plastics, metals and alloys, and composite materials.
Polymers and Plastics
Polymers and plastics are the most common materials in injection molding. They offer versatility, low cost, and ease of manufacturing. Common plastics like polyethylene and polystyrene have a wide range of applications, from packaging to automotive parts.
Cost-Effectiveness: Plastics are generally cheaper than metals and composites, with prices ranging from $0.50 to $5 per pound.
Molding Efficiency: Plastics can be molded quickly, with cycle times as short as 30 seconds.
Customization: They allow for a broad range of colors and finishes.
Strength and Durability: Certain high-performance plastics can rival metals in strength but often at lower weights.
Metals and Alloys
Metals and alloys, used in metal injection molding (MIM), cater to applications requiring high strength and thermal resistance. Stainless steel, titanium, and aluminum are popular choices.
High Performance: These materials withstand extreme temperatures and mechanical stress.
Precision Manufacturing: MIM achieves high precision, suitable for complex components like surgical tools.
Cost Implications: The cost is higher, with materials like titanium costing upwards of $20 per pound.
Longevity: Metal parts often have longer lifespans, enhancing the product’s overall value.
Composite Materials
Composite materials in injection molding are gaining popularity for their strength-to-weight ratio and customizability. They combine materials like glass or carbon fibers with a polymer matrix.
Enhanced Properties: Composites offer improved strength and stiffness, often crucial in aerospace and automotive industries.
Variable Costs: The price can vary greatly, with carbon fiber composites costing between $10 and $60 per pound.
Design Flexibility: They allow for innovative designs unachievable with traditional materials.
Environmental Considerations: Composites can be challenging to recycle, impacting their long-term environmental footprint.
Each material category in injection molding brings distinct advantages and challenges, influencing the choice based on the specific application. For detailed information on each material, its properties, and applications, you can visit Injection Molding Materials on Wikipedia.
Injection Molding Processes
Injection molding, integral to manufacturing numerous products, encompasses various processes. Each process offers unique capabilities and suits different applications. This section delves into conventional injection molding, gas-assisted injection molding, and structural foam molding, highlighting their features, advantages, limitations, and cost implications.
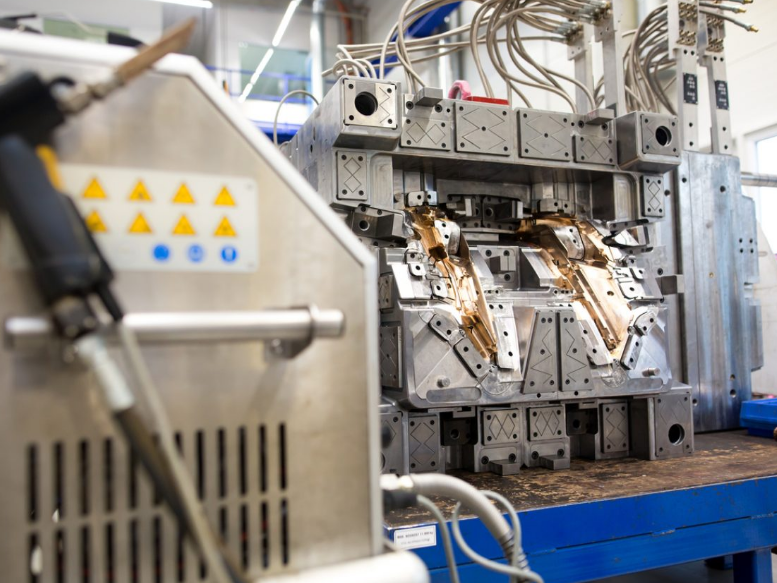
Conventional Injection Molding
Conventional Injection Molding is the standard in the industry, known for its reliability and efficiency. This process suits a broad range of products, from small components to large parts.
High Efficiency: It typically has a cycle time ranging from 15 to 60 seconds, depending on part complexity.
Versatility: This process works with a vast array of materials, from common plastics to specialized polymers.
Cost Factors: The initial investment can be significant, with machinery costs ranging from $30,000 to $500,000.
Quality and Precision: It produces high-quality parts with excellent surface finish and dimensional accuracy.
Gas-assisted Injection Molding
Gas-assisted Injection Molding introduces a gas (usually nitrogen) into the molten polymer to create hollow sections within the part. This technique reduces weight and material usage.
Reduced Material Costs: The use of gas can reduce material usage by up to 30%.
Enhanced Strength: Hollow parts maintain strength while reducing weight, beneficial in automotive and aerospace applications.
Complexity and Cost: The process is more complex and requires specialized equipment, often increasing the overall cost.
Structural Foam Molding
Structural Foam Molding involves injecting a foaming agent with the plastic. This process creates a cellular core with a solid skin, offering enhanced strength-to-weight ratios.
Lightweight and Strong: Parts are lighter yet strong, ideal for structural applications.
Material and Energy Efficiency: This process uses less material and often requires lower clamping forces, reducing energy consumption.
Cost and Flexibility: While the process can save on material costs, the specialized equipment and slower cycle times can increase overall production costs.
Each of these injection molding processes offers unique benefits and is suitable for specific applications. Manufacturers choose a process based on the requirements of the product, balancing factors like cost, material properties, and desired product characteristics. For comprehensive insights into these processes, explore Injection Molding Processes on Wikipedia.
Applications of Different Injection Molding Types
Injection molding plays a crucial role in various industries, each with distinct requirements and challenges. Here, we focus on the applications of injection molding in the automotive industry, medical equipment, and consumer products, providing a detailed analysis using a comparative table format.
Industry/Application | Automotive Industry | Medical Equipment | Consumer Products |
---|---|---|---|
Materials Commonly Used | Polypropylene, ABS, Polyurethane | Medical-grade plastics, Silicone | Polystyrene, Polyethylene, PVC |
Typical Products | Bumpers, dashboards, light housings | Surgical tools, implants, diagnostic devices | Toys, household items, electronic casings |
Quality Requirements | High durability, heat resistance | Sterilizability, biocompatibility, precision | Aesthetics, durability, cost-effectiveness |
Production Volume | High volume, consistent quality | Low to medium volume, high precision | High volume, diverse designs |
Cost Considerations | Moderate to high: Material and precision molding increase costs. | High: Specialized materials and precision increase costs. | Variable: Dependent on product complexity and material. |
Advantages | Durability and safety: Automotive parts require materials that withstand mechanical stress and high temperatures. | Precision and safety: Medical devices demand high precision and compatibility with human tissue. | Design flexibility: Consumer products benefit from a wide range of colors, textures, and shapes. |
Challenges | Balancing cost with material performance | Adhering to strict regulatory standards | Catering to rapidly changing consumer preferences |
In the automotive industry, injection molding is essential for producing parts that are durable and able to withstand high temperatures and mechanical stress. The medical equipment sector demands materials that are sterilizable and biocompatible, with a focus on precision and safety. Consumer products vary widely, requiring materials that are cost-effective and versatile in design.
Each sector leverages the strengths of injection molding to meet specific needs, balancing factors like cost, material properties, and production efficiency. For further information, delve into Injection Molding Applications on Wikipedia.